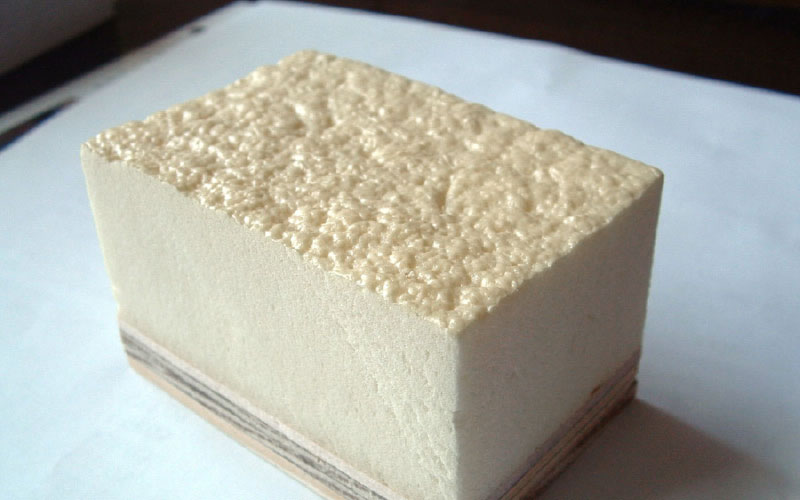
Sprayed Polyurethane Foam is a combination of isocyanate and polyol. These two components are fed through a proportioner which heats then pumps the two separate components to the spray gun, where they are mixed and sprayed onto the substrate.
Because it is sprayed onto the roof as a liquid, it forms a single continuous structure that is seamless and very stable. SPF requires a clean surface for proper application. It must be dry, free of contaminants like oil, and properly fastened to the substrate in accordance with the proper building codes.
A protective elastomeric top coat (Acrylics, Silicones or Polyureas) is required which is typically sprayed on as well, but it is also possible with some to be applied with hand or power rollers.
Foam roofing has many advantages over traditional roofing methods, and as you read through this web site you will learn a lot more about them.
Here are some brief examples:
Seamless Polyurethane foam is applied as a liquid, creating a single monolithic membrane that covers the entire roof. There are no seams or joints, the source of the majority of leaks in traditional roofs.
Flexible: The foam can be sprayed onto virtually any surface, irregularly shaped roofs and protrusions are readily taken care of.
Lightweight: Foam roofing typically weighs around 50 lbs. per square, versus 800 lbs. for a built-up roof and 100 lbs. for ballasted single-ply roofs.
Thermal Insulation: SPF has the best insulating properties available for commercial construction today.
Sustainability: Foamed roofs require a minimum of upkeep, creating little waste and have an indefinite lifespan.